
Is your laboratory safe and fit for purpose?
By Suzanne Jordan - 30 September 2011
Microbiological analysis needs to be closely controlled for the user of the results to have confidence in their reliability. Part of that control is ensuring that the laboratory is suitable for purpose, and provides a safe working environment for all staff and visitors. The design of a laboratory will depend on the type of analyses it 'is used for as this will determine the 'Containment Level' or set controls needed to meet safe working practice.
It doesn't matter if you are building from scratch, adding to an existing facility, or merely upgrading it: the end result has to meet the need. But what are the factors that really matter? Well, a quick look at the relevant areas of legislation will give you a clue to those that affect the workforce: from general Building and Construction Regulations through the Workplace (Health, Safety and Welfare) Regulations to fire regulations and microbiology containment requirements, there is an awful lot to take into consideration. And then you need to ensure that the workforce can carry out the analyses effectively!
As well as building construction, you have to consider the safe installation and correct working of equipment. We have identified 33 different types of equipment commonly in use in most laboratories that need to be evaluated! – . When you have the facility up and running, don't forget to document your procedures regarding access to the facility, training, cleaning and disinfection, transport and handling of cultures and waste media, washing of lab coats, and general risk assessments and handling of hazardous substances. Last and by no means least, you'll need to keep a record of your emergency procedures as well.
There are additional considerations to take into account if you are using a portable or temporary building, and yet more if you are extending, refurbishing or upgrading an existing facility – mainly related to the measures that have to be taken to avoid disrupting or compromising ongoing work.
Few would attempt to build or refurbish a microbiology laboratory without expert advice. It is something we often get asked to help with. So much so that we have published a new guideline (Guidelines for the design and safety of food microbiology laboratories – Guideline No. 66) which specifically covers laboratories up to Containment Level 2.
If you are building, refurbishing or setting up a lab, the many practical tips in this guide could save you considerable time and money. And if you need a tailored approach to lead you through step–by–step, we will be pleased to help.
Suzanne Jordan
+44(0)1386 842013
suzanne.jordan@campdenbri.co.uk
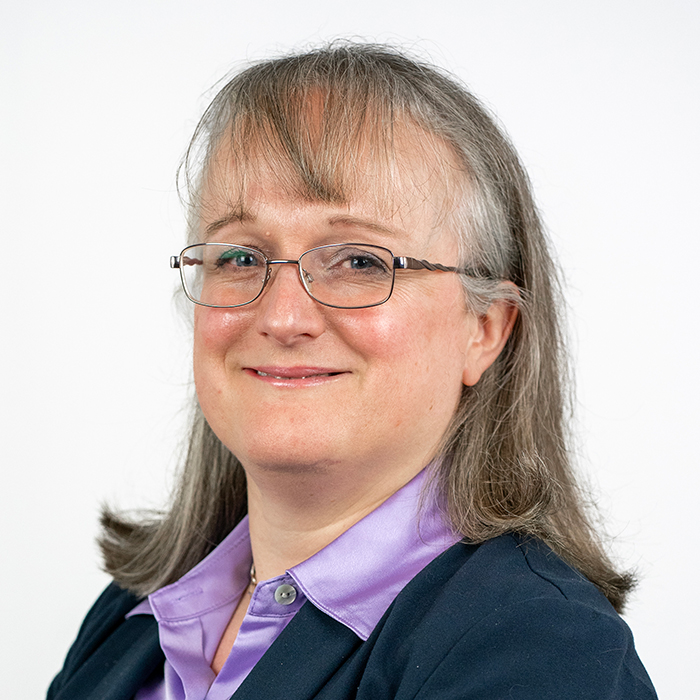
About Suzanne Jordan
Suzanne has worked here at Campden BRI since 2005, following nine years of PhD and postdoctoral research experience in food microbiology and molecular biology of food microorganisms.
Suzanne is the lead for third party microbiological method validation studies for AOAC, MicroVal and NordVal, is a Retailer-approved Method Review Co-ordinator, and is involved in several research and contract projects for developing and evaluating new methodology. Alongside this, she is an industrial PhD supervisor for a project on the of fine-tuning dietary fibre to target gut microbiota accessibility.
During her career to date she has participated in multidisciplinary research projects involving European partners, developed expertise in a range of molecular techniques, and presented her research at an international level and in peer-reviewed journals.