
Plastic packaging alternatives – what you need to know
By Lynneric Potter - 30 July 2018
Many industries use plastic in their production and/or packaging systems. The food sector is looking at alternative materials and systems to reduce the use of plastic packaging. Some companies have already pledged to reduce or eliminate plastic packaging, or to ensure it is recyclable. Packaging carries out three main functions: protection, preservation and promotion of the product. The challenge is to find a replacement that does all three and is also cost effective, safe, and looks good.
What are the alternatives to plastic?
There are many plastic packaging alternatives available - from paper and plant-based materials, to those that look and feel like plastic. But there are lots of things to consider when making a change to your packaging, whether you’re substituting plastic with non-plastics, exploring lightweight materials, introducing recycled materials, changing the design or trying to reduce costs.
Choosing the correct packaging is key to ensuring safe delivery of product through the supply chain. Rigorously testing the performance of your packaging materials means you can be assured that your product will remain in top condition throughout its journey from the production line through to consumers’ homes.
Things to consider when changing your packaging
There are a number of tests available that can be used during the design and manufacture of packaging to test its ‘fitness for purpose’.
- Compression testing determines the vertical load which can be applied. We use this test for distribution packaging to assess its ability to protect its contents and it can also be used to measure stacking height. This ensures the packs can withstand the compressive force exerted upon them when stacked, but also ensures the material isn’t over specified and therefore unnecessarily expensive.
- Peel testing measures the strength of a package seal. It can be used to assess the force required to peel a lid from a container, and the ease with which the lid can be peeled by the consumer. This is particularly important for the ageing consumer and those with dexterity issues.
- Similarly, tensile testing can measure the strength of a flexible seal to ensure strength and integrity.
- Coefficient of friction, or slip resistance, is important for packaging and is a fundamental property of all materials which run on high-speed printing and packaging lines. We can test the slip resistance to ensure your film doesn’t scuff or jam on the line.
- Gas transmission - especially in modified atmosphere packaging and vacuum packs.
Effect of temperature
You also need to consider the temperature that your product will be exposed to during processing and throughout its shelf life. Is it being reheated? If so, you will need to carry out cooking validation as the thermal properties of different materials vary and may affect the cooking instructions, for example board cannot be heated to as high temperatures as plastic. Or maybe you are exporting the product to countries that have different climates from where your packaging testing was carried out so you will need to test that the packaging can withstand the temperature and humidity without changing its barrier properties. The permeability of films and containers can be measured at a range of different temperatures and humidities to determine their oxygen and water vapour transmission rates.
We’ve been working with the food and packaging industries for many years to ensure their packaging is fit for purpose, or to reduce cost and environmental impact. To find out more about how we can help you switch from plastic packaging to alternatives, or for any packaging NPD or trouble shooting please get in touch.
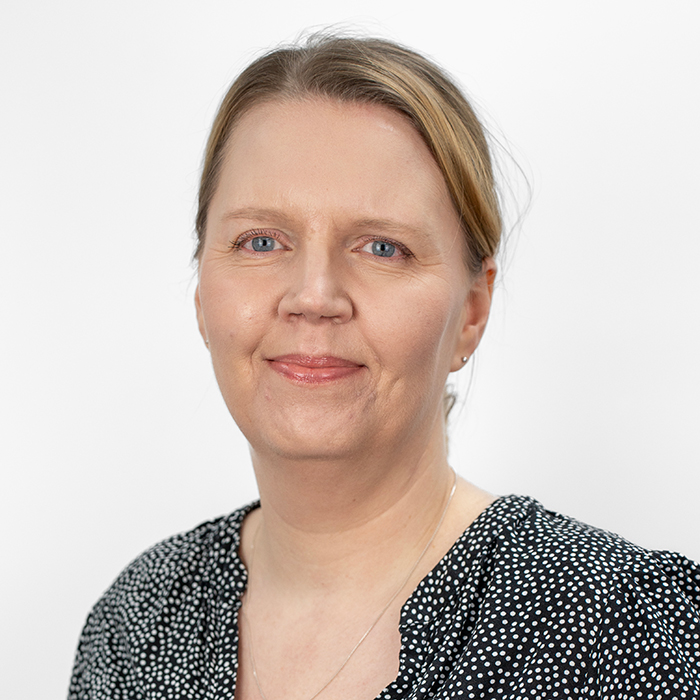
About Lynneric Potter
Lynneric has worked at Campden BRI since 1999, and has spent the majority of this time specialising in all things packaging, including supporting members and clients, managing contract projects, and conducting research.