
Single-use plastic packaging challenges
By Lynneric Potter December 2019
Whilst there has been a huge media and consumer focus over the past year regarding plastic, particularly single-use plastic, there isn’t a single solution or clear route to reducing the amount of plastic used or even to replacing it. Indeed, from the stance of technical performance of the product, replacing it isn’t necessarily the right route for all applications. The many images of plastic swamping rivers and the sea clearly show there is a major problem that needs to be addressed. However, as in any situation, the problems need to be analysed rigorously and offset against the benefits. A whole range of different foods and drinks are packed in plastic packaging - protecting it during transport, helping reduce food waste and providing convenience.
Sustainability can have many meanings within a business and consumers may have an entirely different understanding. Many materials are now being proposed as alternatives to plastic. Given the many properties that have made plastic the packaging success it has become, it is important to understand the technical challenges with reducing or replacing plastics. It is not simply a case of swapping to something else - there are many technical considerations.
We’re currently undertaking a member-funded project to investigate the technical challenges of reducing or replacing single-use plastics for food and drink. As part of the study, different businesses along the supply chain, including packaging manufacturers, food and beverage manufacturers, packers, retailers, waste management companies, and consumers have been discussing what their technical challenges are.
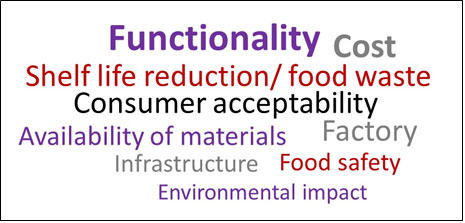
The main and most common challenge for participants was the functionality of alternative materials compared to plastics.
Functionality of alternative materials
Concerns with functionality of alternative materials include meeting the barrier properties such as the oxygen and moisture transmission rates, general strength of the material, clarity, sealing properties and integrity, and impact of temperature exposure - both high and low. Collectively these factors play a role in preventing spoilage, physically protecting the product from damage, and visibility of the product to consumers, as well as determining the compatibility of the product, process and packaging material. It is likely that some of these will need to be compromised when an alternative material is introduced. The quality of the plastic alternatives being produced was also considered a key concern and unlike plastics, there are currently no regulatory rules governing many of these. An additional consideration was that there will be very little data and literature available on how some of these new materials behave, their interactions with food, and whether in the longer term their use might also prove to be as contentious for reasons which may become apparent in the future.
Cost
Cost was also one of the top challenges – in particular the cost to manufacture and purchase alternative materials and whether it could be passed on to the consumer. Put simply, will consumers be able and/or prepared to pay more for a product if the alternative packaging costs more? Studies indicate that when asked, they say they would. A consumer study carried out for Marketing Week showed that 60% of consumers would choose the sustainable option if it provided the same convenience and was the same price as its equivalent. However, only 14.6% would purchase the sustainable option regardless of convenience and cost.
Shelf-life and food waste
Food manufacturers are constantly striving to extend the shelf-life of their products to provide convenience and minimise waste. This can be difficult with the requirement to produce foods with a ‘clean label’, reducing the number of additives and preservatives previously added to foods. Shelf extension means the product can have more time in distribution, on the shelf and with the consumer. Foods can be transported further, meaning greater opportunities for export and covering longer distances. When using any new material, shelf-life needs to be re-established and if using alternative materials this may not just be assessing the shelf-life of the food packed within but also the packaging material itself. Shelf-life of a product may include microbiological testing and quality checks but the same may apply to the material. Its functionality, and abuse of the packaging should be included for unexpected scenarios.
Consumer acceptability
Consumers can often make purchasing decisions from packaging, as it gives a first impression, so consumer acceptability of alternative materials is going to be key. There would be little incentive to pack a product in a material with all of the sustainability credentials if the consumer is not going to purchase it. Other challenges include meeting the consumer’s desire for convenience, how to inform the consumer about the materials themselves and also providing guidance on how best to dispose of them.
Availability of materials
Another challenge for the packaging industry is whether it can meet the supply demands required of alternative materials and whether there will be enough raw material available to allow manufacture at the required scale. A great deal of trial and error is required in the development of new materials. The push to develop plastic alternatives has been ongoing for many years, well before the ‘Blue Planet II’ highlighted the issues in 2018.
To bring a material to the market that could be used in place of plastics is a difficult and lengthy process. As well as the functional aspects of any new material, compliance with the regulatory requirements also need to be considered.
Ethical considerations also arise – is it acceptable to use land to grow crops for packaging rather than food?
Within the factory
Alternatives may also mean that changes to factories and equipment are necessary, creating further technical challenges. If a packer is going to change material, there can be a huge cost implication. A change of material will require modifications to the production line and investment in new sealing heads. There could also be a change in throughput, logistics and shelf-life. When supplying globally, with different capabilities, the same product may be packed in a number of different formats or sizes. There is also the challenge of hygiene in the factory and whether alternative materials could support the growth of microorganisms.
Infrastructure and waste management
A huge investment is required in infrastructure to be able to collect, sort and recycle the materials we are currently using. At present there are different infrastructures within and across countries. The big question coming from our research so far is: “Who is going to fund the infrastructure required?”.
The increase in biodegradable and compostable materials on the market with limited collection facilities means these materials will go to landfill or incineration, where there is no collection infrastructure for them. This will mean that they move further down the waste hierarchy pyramid or even worse contaminate other waste streams. Obviously, neither of these is desirable. Misconceptions also need to be overcome; if a material is labelled as biodegradable it doesn’t necessarily mean that it can be sent to landfill and will imminently breakdown. Additionally, packaging which states that it is ‘compostable’ may only decompose in an industrial composter rather than at home. ‘Zero waste to landfill’ declarations may simply mean all waste has been incinerated rather than sorted and recycled.
The challenge is to make recycling and disposal of materials in the home and on the go simple and convenient.
With waste processing, contamination of waste streams provides sorters and recyclers with major technical challenges. Although there is some confusion over what can and cannot be recycled, this cannot be the only reason for the huge range of non-recyclable materials found in household recycle bins. For example, animal waste, sanitary products and nappies, car parts, flexible plastics and food are regularly found at recycling plants, leading to the rejection of batches of materials sent for processing. Clearly, the problems associated with recycling are many – achieving compliance with specific requirements is challenging on many levels.
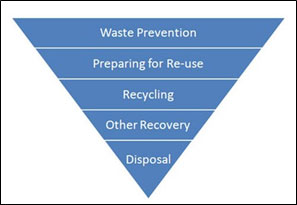
Life cycle analysis
Life cycle analysis of alternative materials was also noted as a challenge. Businesses could go down the route of changing material without consideration of the environmental impact of the new material beyond whether or not it uses less plastic. When performing life cycle analysis what should be measured? Carbon footprint? Water? Energy? And how far back in the packaging supply chain should we go in the life cycle assessment if the material is a by-product of other processes? It is also not clear yet what impact using non-plastic materials will have on the environment.
Ready meal packaging study
As part of our project, we tested the functionality and properties of alternative ready meal packaging materials (bagasse, paperboard and aluminium) alongside conventional plastic (CPET) in terms of container strength, integrity and barrier properties in different storage environments. Interestingly, drop tests showed that aluminium and paperboard trays performed better than the plastic trays. We presented the results at our Packaging MIG meeting which provided members with an insight into the potential of these alternative materials.
Further case studies will be examined as our ‘Replacing single-use plastics’ project continues. Have any ideas? Tell us what cases you would like us to study and help steer the project towards your needs.
What next?
As we can see, there are many technical challenges to reducing or removing single-use plastics. With the ban on single-use plastics coming into effect in the EU by 2021, there isn’t a great deal of time to overcome them. However, should we be comparing alternative materials to plastics and have the same expectations? Should we be expecting the same shelf-life of a product if we are not using plastics? With a whole range of alternative materials to plastic becoming available, the industry needs to ensure that food and packaging materials are compatible and also be aware of their environmental impacts. Ultimately manufacturers and retailers want to deliver safe foods to the consumer, but there are many hurdles to overcome.
This article was first published in Baking Europe.
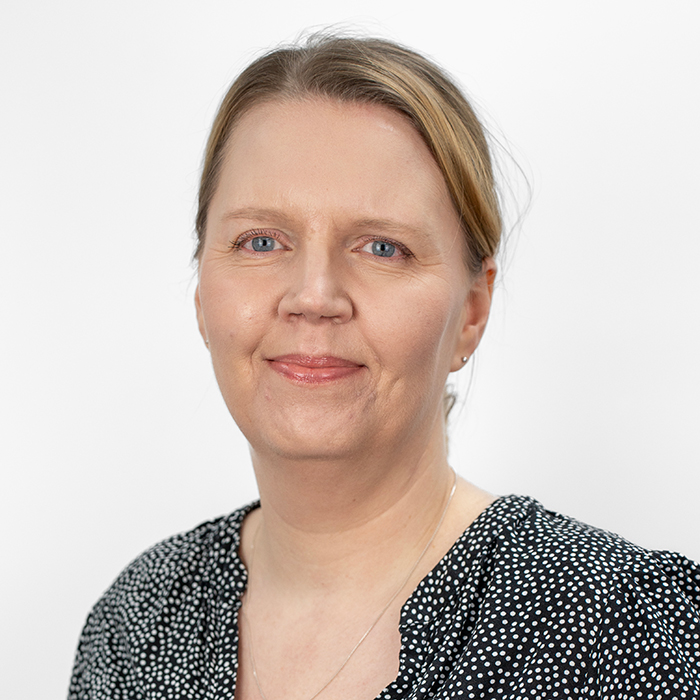
About Lynneric Potter
Lynneric has worked at Campden BRI since 1999, and has spent the majority of this time specialising in all things packaging, including supporting members and clients, managing contract projects, and conducting research.