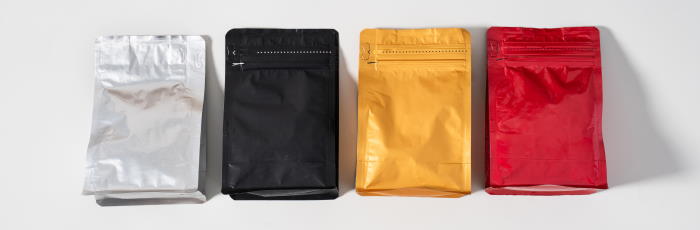
Flexible mono-materials packaging challenges
6 December 2021 | Lynneric Potter, Food Packaging Technical Lead
As of April 2022, a new tax on plastic packaging will be introduced, affecting packaging manufacturers, importers, business customers, and consumers of plastic packaged goods in the UK. The aim of this is to drive down the use of virgin plastics and packaging that contains less than 30% of recycled plastic. The rate of the tax will be £200 per tonne of plastic packaging, with anything where the heaviest component is plastic being included in this taxable bracket.
Whether this tax creates a meaningful environmental benefit or not is yet to be seen. Since the production of plastic began in the 1950s, a significant amount of UK plastic has ended its lifecycle as waste. A situation that is reflected in many countries, on a global scale.
What are the considerations of packaging?
Firstly, it is important to appreciate the role that food packaging plays and some of the attributes it requires to function as expected. The main purpose is that it maintains the quality and safety of the product contained within by providing a barrier to contamination, gases, and moisture. It must do this whilst being suitable for product characteristics, being able to withstand high temperatures if processed, and having the integral strength to be handled and transported. During its life a package may meet extreme conditions, in that it will be exposed to a range of temperatures and humidity levels in storage and subjected to a microwave or oven by the consumer. It must be fit for purpose, whilst complying with regulations.
Recyclability: Mono vs multi layers flexible packaging
Flexible multi-layered packaging types have a fair amount going for it. They have low production and transportation costs, are light in weight and light in material use. The various materials it can contain, such as polyester, aluminium, polyamide, and polypropylene, have varying individual capacities to prevent the penetration of oil, oxygen, and moisture, helping reduce food waste by improving shelf-life.
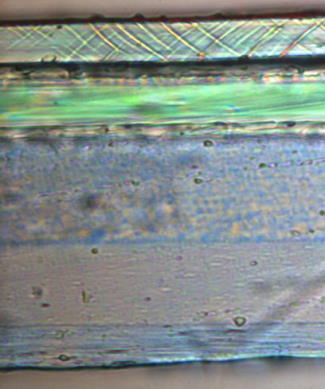
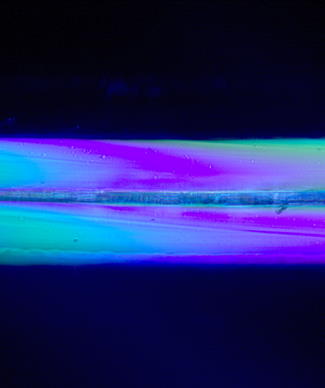
These materials can be used altogether or in different configurations to achieve specific packaging properties, such as: the ability to withstand pasteurisation and sterilisation temperatures; mechanical strength against puncture, tearing and dropping; the ability to act as a barrier; the capacity to be microwaved or passed through a metal detector; and aesthetic characteristics, including transparency, high gloss, and a printable surface. The problem is that the layers are often laminated together and, therefore cannot be recycled using traditional recycling methods, making flexible mono materials packaging an easier to recycle than multi-layer packaging.
So, how can improvements in packaging help this?
In recent years, the need to recycle whilst maintaining the useful properties of multi-layered packaging has caused a shift in focus towards mono-material packaging. Also known as single polymer plastic, mono-material packaging can be made of PE, PP, or PET, as well as a small proportion of adhesives, inks, and other additives. With most recycling centres equipped for PE, PP, and PET, the use of mono materials makes collection, sorting and recycling more efficient.
Although, mono-material plastic is easier to recycle, its use in packaging may require more material than the equivalent multi-layered package. Mono materials may need to be thicker, have a coating, or have a thin laminated layer of another material to provide the desired properties.
How can we help?
Traditional mono-material packaging requires refinement to ensure that they perform at the same level as multi-material counterparts, by offering a sufficient barrier, to ensure product safety and quality is maintained, as well as meeting consumer needs in terms of functionality and aesthetic experience.
Campden BRI can help with transition from multi-layered material to mono-material, and the evaluation of new packaging formats by assessing seal strength and integrity. Our burst, creep and tensile test will help to determine the strongest and weakest points within the seal area whilst the penetrant dye test can detect leaks smaller than 100µm. We can assess material strength by using puncture and elongation test methods, whilst analysing the co-efficient of friction to help understand how the material will run on the line. In addition, oxygen and moisture permeation can be checked to assure suitability of the material for the product, process and desired shelf life. We can also offer comprehensive storage trials in various conditions, supported with sensory evaluation, determination of microbiological shelf life of the product, and necessary migration testing.
Contact our expert, Lynneric Potter to discuss your innovative solutions and to discuss the possible impacts of using mono-material packaging for a range of applications.
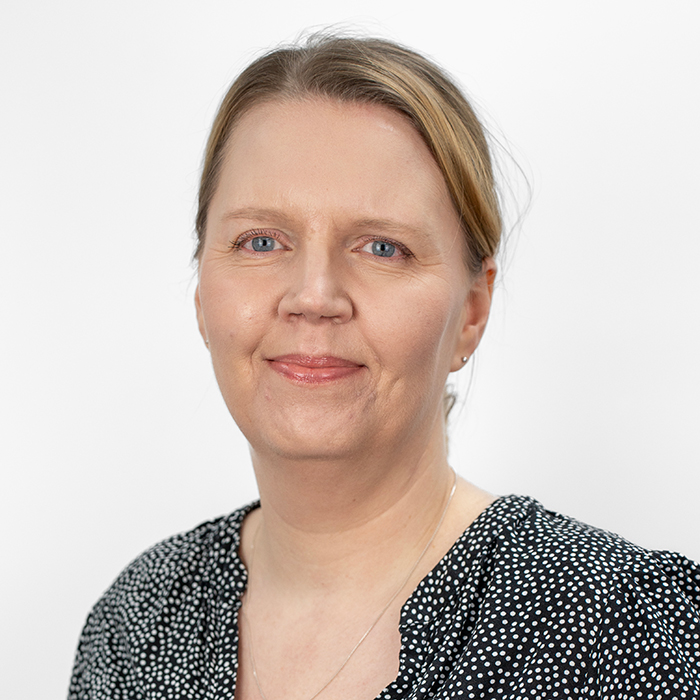
About Lynneric Potter
Lynneric has worked at Campden BRI since 1999, and has spent the majority of this time specialising in all things packaging, including supporting members and clients, managing contract projects, and conducting research.
Food packaging plastics testing
Visit our Food packaging plastics testing page to find out about some of our other packaging services
Need help in this area?
Campden BRI offers independent analysis as part of a wider testing regime if required. Our range of complementary methods are available to assess whether your packaging is fit for purpose, including strength and integrity testing.